Balancing Act: CMO Maximizes Cold Storage Capacity While Minimizing Energy Use
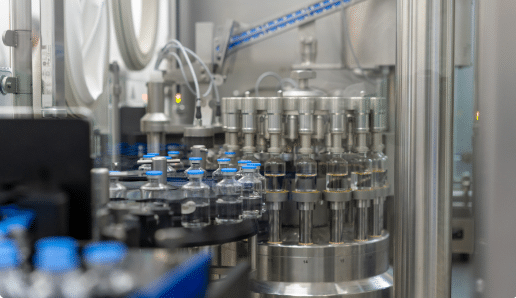
Xpress® enabled a leading pharmaceutical contract manufacturer (CMO) to expand cold storage by 66% to meet vaccine demand without a proportional energy increase.
$560,000
in avoided energy costs
20%
improvement in chiller plant efficiency
location
400,00 sq. ft.
size
4,500 tons capacity
industry
Pharmaceuticals
the problem
Balancing Growth, Energy Efficiency, and Cost Control
A leading CMO in the Northeastern United States faced a significant challenge when expanding its cold storage capacity to meet increased vaccine production demands from multiple clients. This 66% expansion in cold storage space threatened to dramatically increase energy costs at the 400,000 sq. ft. research and production facility. The CMO needed to ensure their chiller plant could efficiently manage the additional cooling load from the expanded cold storage without proportionally increasing energy consumption and operational costs, which would impact both their profitability and competitive pricing for client manufacturing contracts.
the solution
Seamless BAS Integration
The site implemented the tekWorx Xpress® optimization system, integrating it with their existing building automation system (BAS).
The Xpress® optimization solution delivered three core improvements:
- Dynamic Chiller Management: The system’s adaptive algorithms continuously adjusted chiller operation based on real-time cooling demands, significantly improving efficiency curves across all chillers to effectively manage the increased load requirements.
- Optimized Water Distribution: By converting to a variable primary flow system, the facility achieved more efficient distribution of chilled water to cold storage areas, allowing primary and distribution pumps to operate at optimized speeds that reduced energy consumption while maintaining critical temperature stability.
- Intelligent Load Response: The system effectively managed load fluctuations from cold storage door openings and product movements, ensuring temperature consistency during operational variations without excessive energy use.
This balance between maximizing capacity and minimizing energy use has been transformative for our operations, especially as vaccine production demands continue to grow.
Site Facilities Engineer
This comprehensive approach allowed the facility to address both the immediate challenges of the expanded cold storage capacity and establish a foundation for long-term efficiency in their critical cooling operations. The integration with existing systems ensured minimal disruption while delivering immediate optimization benefits from day one of implementation.
the results
Meeting Increased Cooling Demand with Minimal Energy Impact
tekWorx holistic optimization approach allowed the facility to absorb the increased cold storage demand with minimal impact on overall energy consumption. Despite a 25% increase in overall cooling load due to the cold storage expansion, total chiller plant energy consumption increased by only 5%. This remarkable efficiency meant the facility avoided $560,000 in projected additional energy costs associated with the cold storage expansion.
These results demonstrated that with the right optimization approach, facilities can significantly expand cold storage capacity without accepting proportional increases in energy consumption.