Milwaukee Beverage Manufacturer Brews Up Big Energy Savings
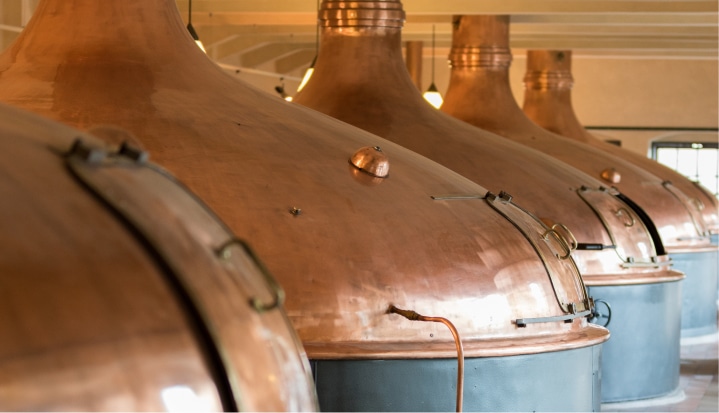
A leading Milwaukee beverage manufacturer transformed its outdated chiller system into an efficiency powerhouse, reducing costs and environmental impact while maintaining full production capacity.
750,000
gallons of water saved
472,600
kWh saved annually
location
Milwaukee, WI
size
1,000 tons capacity
industry
Food & Bev
the problem
Inefficient Chiller Operations Undermine Energy and Water Performance
Operating with a traditional Primary/Secondary hydronic design, the system suffered from low temperature differential and required manual operation of two 500-ton chillers. Despite having a Metasys building automation system in place, it lacked optimization capabilities, resulting in excessive energy and water consumption.
Facility managers recognized these inefficiencies but needed a solution that wouldn’t disrupt their continuous production schedule or require substantial capital investment in new equipment. With no real-time monitoring available, they couldn’t effectively track performance or identify opportunities for improvement, making it difficult to justify and measure the impact of potential upgrades.
the solution
Efficiency Without Disruption: Leveraging Existing Infrastructure
tekWorx implemented a comprehensive upgrade strategy that preserved existing infrastructure while maximizing efficiency gains. The approach focused on optimizing existing systems rather than costly replacements.
Key solution components included:
- Converted to an Integrated Primary/Secondary® design to increase the temperature differential
- Integrated the tekWorx Xpress® optimization system with the existing BAS, enabling adaptive control algorithms that continuously adjust chiller sequencing, pump speeds, and setpoints based on real-time conditions, production demands, and weather forecasts—all while maintaining the facility’s existing control infrastructure
- Retained all existing equipment and wiring
- Installed an Energy Efficiency Performance Dashboard for real-time monitoring
This project proved you don’t need to replace equipment to achieve significant efficiency gains. Smart optimization of existing systems delivered results that exceeded our expectations.”
Plant Manager
the results
From Underperforming to Leading the Pack
The tekWorx optimization project delivered significant value across the facility’s operations. By implementing the Xpress® chiller plant optimization system and converting to an Integrated Primary/Secondary® design, the beverage manufacturer achieved remarkable improvements in energy efficiency. The facility now benefits from complete real-time visibility into system performance, enabling proactive management of chilled water equipment, while the enhanced system operates with greater reliability and reduced maintenance needs.
Notable results include:
- Zero production interruption during implementation with all existing equipment and wiring preserved
- $42,000 annual energy cost savings, complemented by a $36,000 utility rebate
- Over 750,000 gallons of water and 472,600 kWh of electricity saved annually