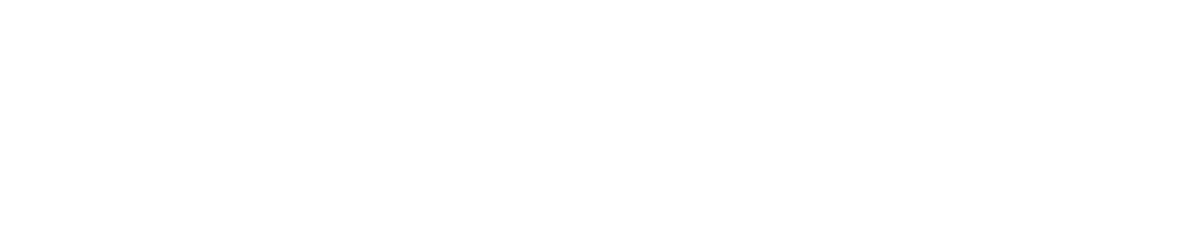
Stellantis HQ Achieves 28% Cooling Cost Reduction Through Plant-Wide Optimization
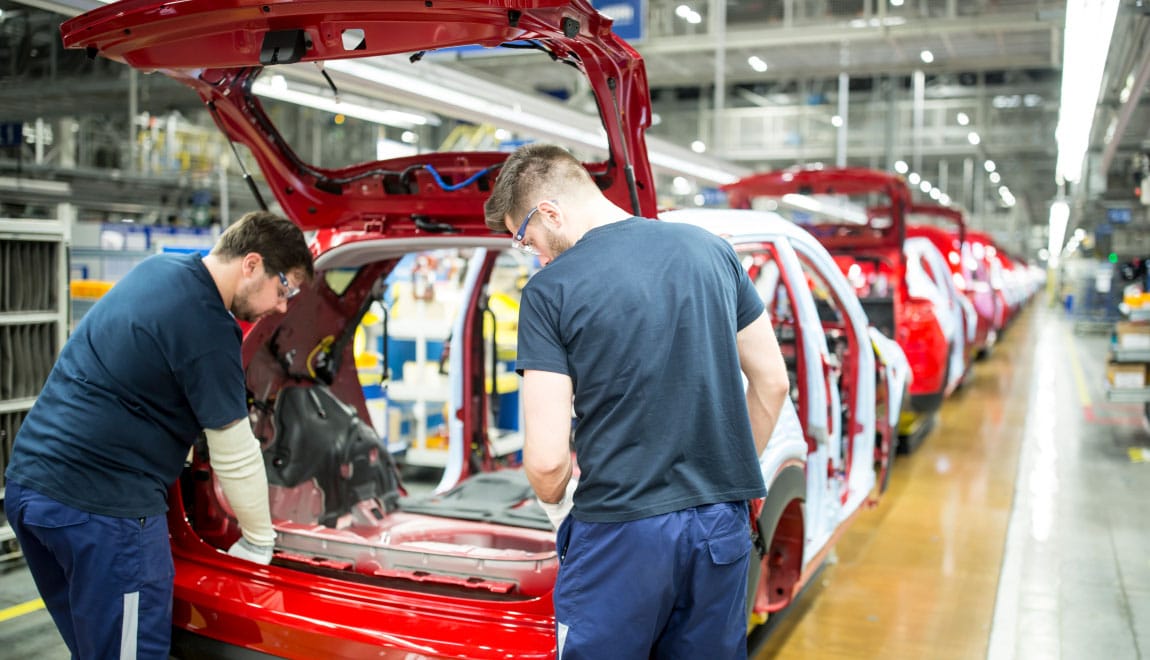
tekWorx optimized existing chilled water infrastructure to deliver major energy savings at Stellantis’ largest North American facility.
28%
annual reduction in energy expenses
12,130,000
kWh saved annually
location
Auburn Hills, MI
size
17,640 tons capacity
industry
Auto Manufacturing
the problem
Aging Controls Drive High Energy Costs
Stellantis’ North American headquarters in Auburn Hills, Michigan, houses critical operations across its expansive 5.3 million square foot campus. Supporting 13,000 employees and maintaining continuous operations for corporate, R&D, and data center functions, the facility’s cooling infrastructure faced significant challenges. The existing system, comprising fourteen chillers with 17,640 tons of total cooling capacity, operated well below optimal efficiency.
Outdated controls required constant manual oversight, while the chilled water system struggled with inefficient flow management through two 3-million-gallon storage tanks. The combination of constant speed primary pumps with balance valves, improperly controlled secondary pump VFDs, and unnecessary chiller operation resulted in poor system performance, characterized by low chilled water temperature differentials (ΔT) and high kilowatt-per-ton ratios.
the solution
Strategic Controls Upgrade Optimizes Plant-Wide Performance
To address these challenges, the facility engineering team partner with tekWorx. The tekWorx team developed a comprehensive optimization strategy that focused on both system optimization and operational efficiency. The cornerstone of this approach was the transformation of the chilled water distribution system and the implementation of advanced controls technology. Rather than continuing with the existing inefficient configuration, the team designed a solution that would maximize the use of the storage tanks while minimizing energy consumption.
The implementation process was carefully orchestrated to minimize disruption to the facility’s critical operations, with the team working closely with facility operators to ensure a smooth transition from manual to automated control. The new control system was designed with redundancy in mind, while the integration of the Xpress® system with the existing building automation system created a unified platform for system management.
The comprehensive solution included:
- Implementation of full variable flow chilled water system for dynamic load response
- Redundant PLC and adaptive Xpress® control solution integration with BAS
- Strategic thermal storage management to optimize energy consumption
- ROI-driven VFD deployment on pumps and cooling towers
the results
Energy Savings Drive Rapid Financial Returns
The project delivered immediate and substantial financial returns through strategic energy optimization. By implementing intelligent controls and system improvements, the facility secured the maximum utility incentive of $200,000 from DTE Energy while achieving a dramatic 28% reduction in annual energy expenses. The comprehensive upgrade also delivered:
- 12,130,000 kWh reduction in annual electricity consumption
- System efficiency improvement of 0.35 kW/ton
- 1.7-year return on investment
The operational transformation extended well beyond energy savings. The new automated platform revolutionized how the facility manages its cooling systems, delivering lasting benefits:
- Equipment lifecycle optimization through reduced wear and automated maintenance scheduling
- Enhanced system reliability through real-time performance monitoring and adjustment
- Increased operator efficiency by eliminating manual intervention requirements
- Proactive maintenance capabilities through automated system health monitoring
Xpress® seamlessly transformed plant efficiency while maintaining critical 24/7 operations for 13,000 employees. This strategic approach to system optimization created a sustainable solution that continues to generate both immediate savings and long-term operational value.