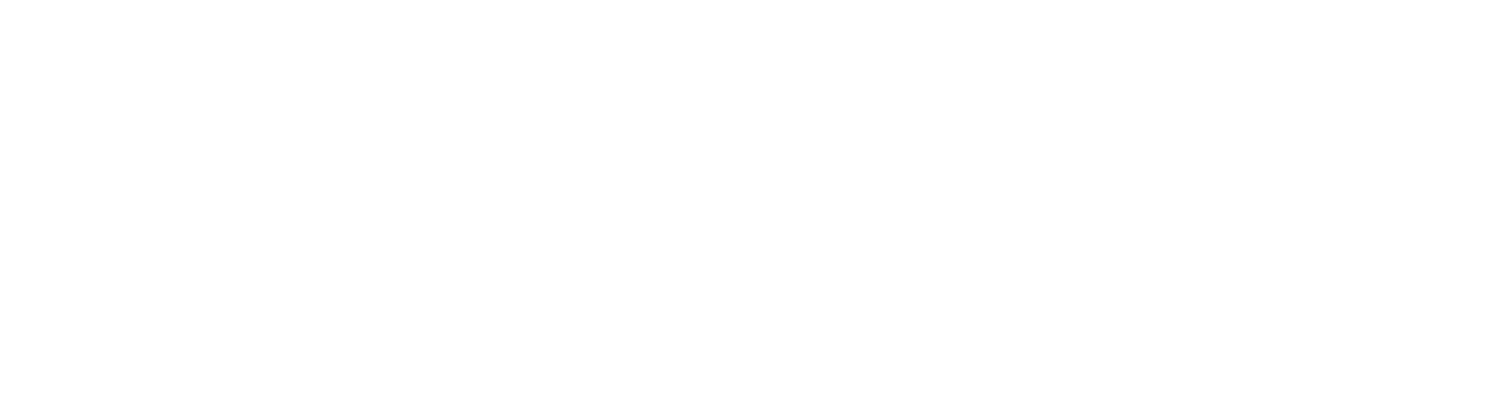
Innovative Cooling Strategy Saves GM Plant $729,000 Annually
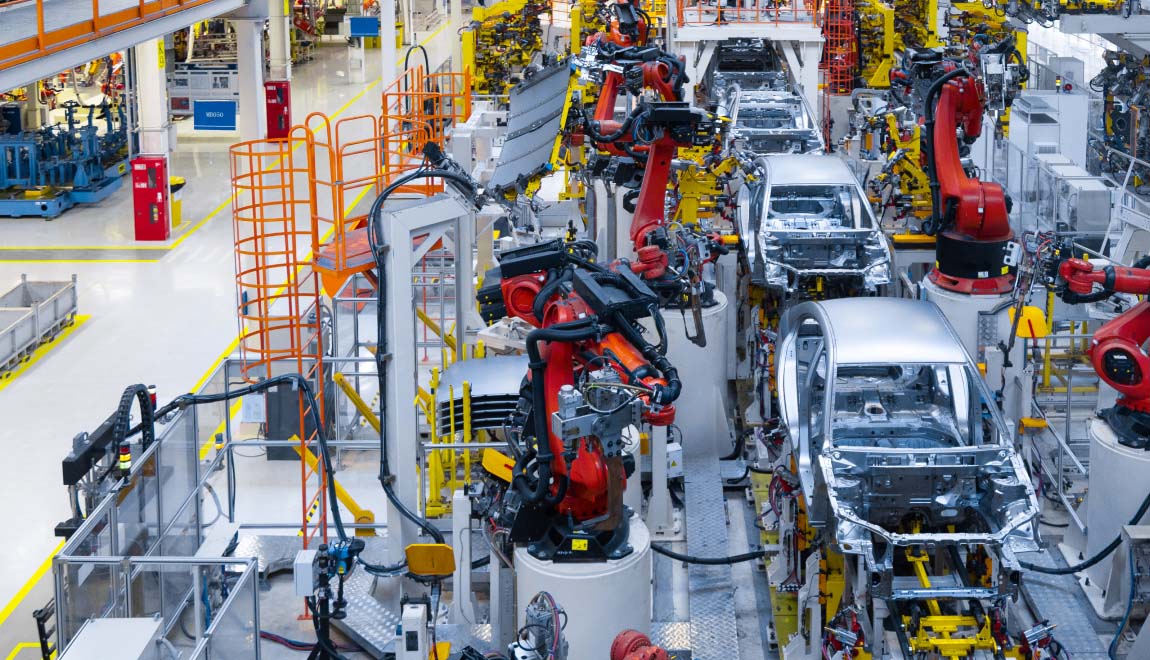
Zero-downtime modernization delivers both stability and efficiency for critical manufacturing operations.
$500,000
TVA Rebate
11,000,000+
kWh saved annually
location
Spring Hill, TN
size
27,000 tons capacity
industry
Auto Manufacturing
the problem
Critical Cooling Infrastructure Optimization
The manufacturing facility’s central plant was responsible for cooling multiple critical production lines representing millions in daily throughput, with any disruption threatening to halt entire manufacturing operations. This mission-critical system required continuous operation, not only for efficiency improvements but to maintain strict production quality standards. The existing Primary-Secondary chilled water system suffered from multiple inefficiencies, including low chilled water temperature differential (ΔT), high energy consumption per ton of cooling (kW/ton), and excessive system pressure.
Further complicating matters, the plant utilized a Programmable Logic Controller (PLC) system that lacked optimization capabilities or automation features, preventing the facility from achieving optimal operational efficiency and stability.
the solution
Seamless System Transformation with Zero Downtime
tekWorx was selected for the optimization project based on their expertise in chiller plant optimization and proven track record of implementing energy-efficient solutions without operational disruption. tekWorx Xpress® platform provides adaptive optimization of chiller plant operations by continuously analyzing system conditions and automatically adjusting equipment sequencing, speed, and loading to maximize efficiency while maintaining precise temperature control.
The comprehensive upgrade strategy enhanced both system efficiency and operational stability and included:
- Conversion to an Integrated Primary-Secondary (IPS)® system with a modulating bypass valve. By eliminating the need for dedicated primary pumps while maintaining hydraulic stability, the IPS® approach reduces capital costs through decreased equipment requirements and minimizes energy consumption by optimizing flow rates to match actual cooling demands.
- Implementation of the adaptive Xpress® system on a new Rockwell PLC platform
- Execution of detailed project planning with a transition schedule avoiding cooling production interruption
Seamless system transformation with zero downtime ensured the 4.7 million square foot manufacturing facility maintained full production capacity throughout the upgrade.
the results
Substantial Savings + Operational Excellence
The control and optimization project delivered both optimal performance and enhanced stability. The comprehensive upgrade generated $729,000 in annual savings and qualified for a substantial $500,000 TVA Utility Rebate. This combination produced an impressive financial return with a 2.8-year payback, or just 1.2 years when accounting for the rebate.
Additional optimization achievements included:
- 11,100,000 kWh saved annually
- .31 kW/ton energy efficiency improvement
- Operators freed for other valuable tasks through automation
The comprehensive tekWorx optimization project delivered significant efficiency gains while maintaining uninterrupted operations throughout the transition process. By integrating the innovative IPS® system with variable flow capabilities and the adaptive Xpress® platform, the facility achieved optimal cooling performance with reduced energy consumption and improved system reliability.