Strategic Xpress® Integration Transforms Energy Consumption at Major Tire Plant
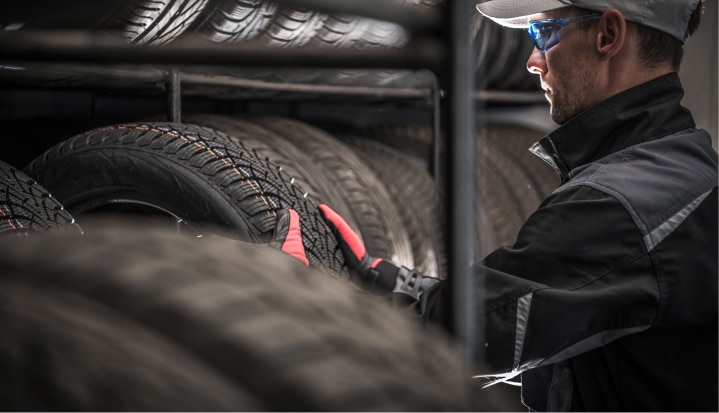
Xpress® technology transformed energy consumption patterns while maintaining production requirements at a major tire manufacturing facility.
$154,000
TVA utility rebate secured
1,544,000
kWh saved annually
location
LaVergne, TN
size
1,200 tons capacity
industry
Rubber & Tire
the problem
Inefficient Cooling in High-Output Production
The Tennessee facility faced significant energy inefficiencies in their cooling systems. The site, which produces truck and bus tires with an output of 7 million annual ton hours, operated 24/7 with extremely limited maintenance windows, making traditional system replacements impractical. The existing cooling infrastructure had several critical inefficiencies:
- A constant flow hydronic design with static chilled water supply temperature setpoint year-round
- Excessive pump power consumption for both condenser water and process chilled water
- High energy consumption relative to cooling output, resulting in unnecessary operational costs
the solution
Seamless Integration with Zero Downtime
Looking to maximize efficiency without disrupting operations, the facility partnered with a recognized leader in HVAC optimization technologies. Xpress® is an intelligent optimization system that dynamically adjusts cooling parameters in real-time, designed specifically for energy-intensive industrial environments where production continuity is critical.
The implementation strategy prioritized both energy savings and operational stability:
- Xpress® technology was seamlessly integrated with the existing Schneider building automation system to ensure maximum cooling efficiency in real-time, maintaining all process requirements at the lowest possible kW/ton
- All existing equipment remained in place, eliminating production downtime
- The standard Xpress® package included an Energy Efficiency Performance Dashboard, eliminating the need for separate monitoring system investments. This system provides real-time monitoring of system performance, including kW and kW/ton metrics for each major equipment piece and the total chilled water system
We maintained 100% uptime throughout the integration while securing immediate financial benefits.
Plant Manager
the results
Cost Savings and Performance Excellence
The implementation yielded impressive returns that validated the strategic investment in energy optimization:
- Optimized cooling efficiency using existing equipment
- Annual energy costs reduced by $93,000
- 1,544,000 kWh saved annually
- $154,000 TVA utility rebate secured
- 3-year project payback period
- Real-time performance monitoring via the Energy Efficiency Dashboard
- Zero production disruption during implementation
The Xpress® solution demonstrates how targeted optimization of existing systems can deliver substantial energy and cost savings while maintaining critical manufacturing operations.