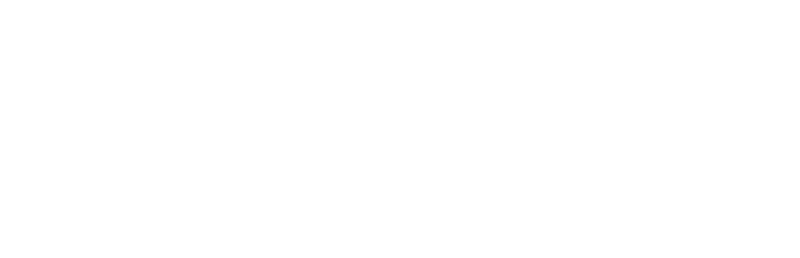
Pharma Chiller Plant Optimization Yields $386,000 Utility Rebate
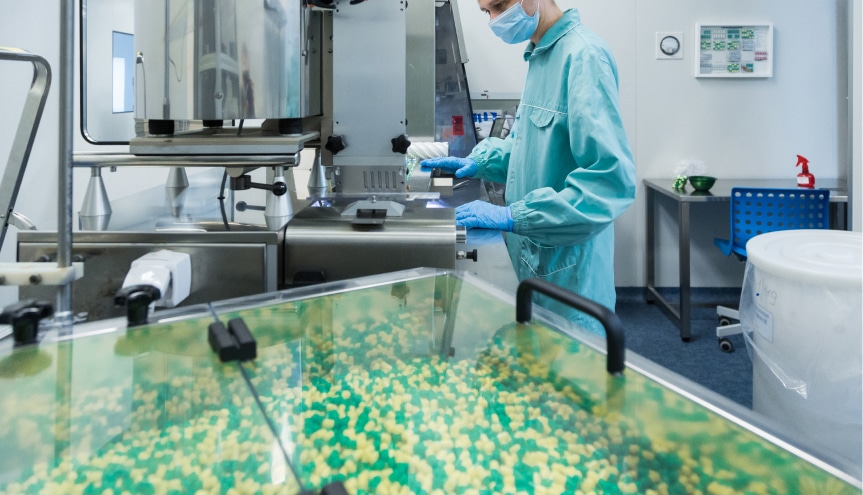
Pharmaceutical R&D campus saved $425,000 annually and secured a $386,000 rebate, with Xpress®.
5,130,000
reduction in annual kWh
$425,000
saved annually in energy costs
location
West Conshohocken, PA
size
10,600 tons capacity
industry
Pharmaceuticals
the problem
An R&D Campus Struggling With Its Chiller Plants
The West Conshohocken facility faced a significant energy inefficiency challenge in its cooling systems. Operating 24/7 to support critical operations, the critical site managed nine chillers of varying sizes and types, providing 10,600 tons of cooling capacity alongside a 1,200-ton free cooling heat exchanger.
The facility operated with an outdated constant flow hydronic design that required manual adjustments to meet cooling demands, severely limiting optimization possibilities. This energy inefficiency was flagged by the corporate Climate Change program as a prime opportunity to both reduce costs and qualify for utility rebates. The situation became more pressing when a new utility contract threatened to increase rates by approximately 50%.
the solution
Addressing Challenges While Maintaining Uninterrupted Operations
Xpress® is an advanced PLC-based control system that optimizes HVAC operations by dynamically managing variable flow systems to match cooling capacity with actual demand in real time. It integrates seamlessly with building management systems to maximize energy efficiency while maintaining reliable performance.
GSK selected Xpress® as the cornerstone of their efficiency initiative. The solution centered on converting the facility to full variable flow operation, with careful attention to maintaining production throughout the implementation process. Additional technical improvements included:
- Installation of VFDs on chilled water pumps
- Implementation of a modulating bypass valve
- Addition of evaporator valves to accommodate different chiller differential pressures
- Integration of VFDs for condenser pumps and cooling towers
Through strategic chiller plant optimization, this pharmaceutical R&D facility secured a$386,000 utility rebateand$425,000 in annual energy savings while enhancing operational efficiency and system reliability.
the results
Utility Rebates Maximize Project Value
The optimization project secured a substantial $386,000 utility rebate from PECO, demonstrating how strategic facility improvements can unlock significant utility incentives. The transformed chiller plant system also generated additional financial benefits:
- Annual energy reduction of 5,130,000 kWh
- Efficiency improvement of 0.41 kW/ton
- PECO utility rebate of $386,000
- Annual energy cost savings of $425,000
Beyond the financial gains, the project delivered significant operational improvements. The facility now benefits from a fully automated system that has freed up staff for other critical tasks while increasing cooling reliability. The lower system pressure has significantly reduced AHU valve maintenance requirements, further enhancing operational efficiency. These operational enhancements continue to provide ongoing benefits that extend beyond the immediate financial returns, improving the overall functionality and reliability of this critical 24/7 pharmaceutical operation.