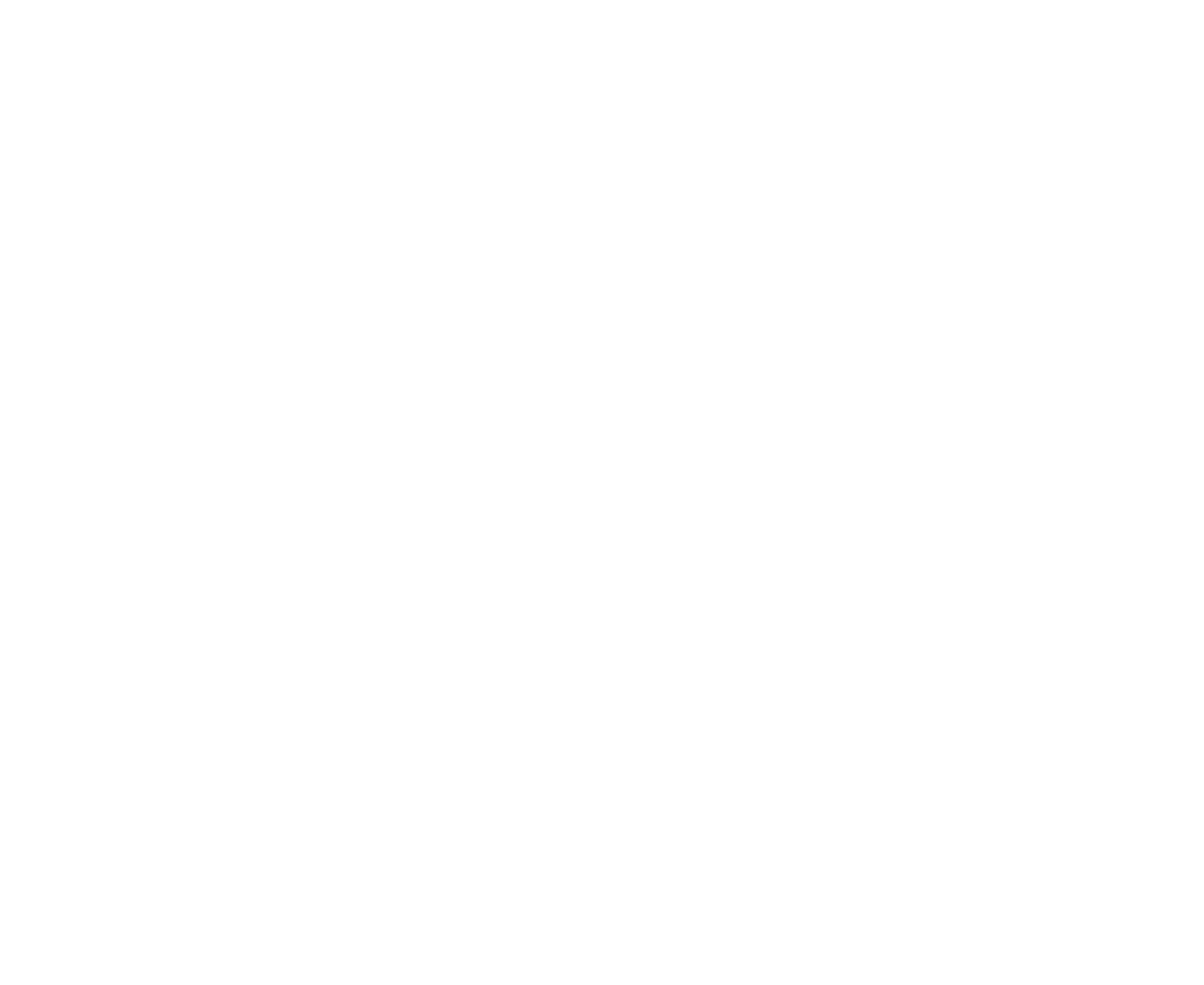
Cooling Optimization Delivers Half-Million Dollar Annual Energy Savings for Nissan
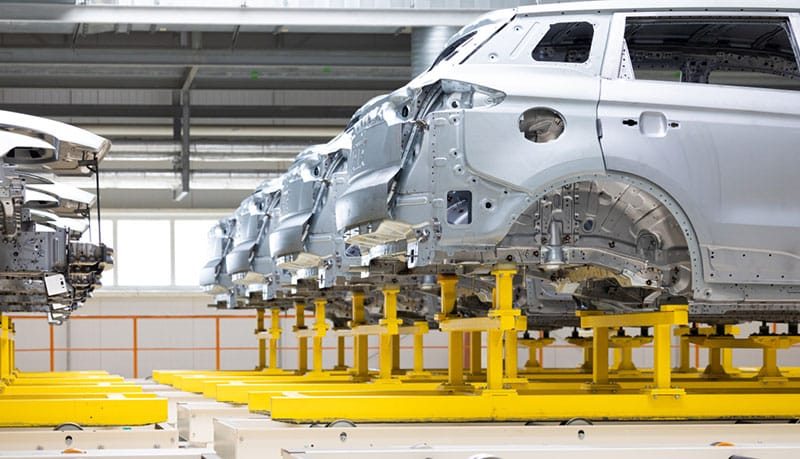
tekWorx delivered $490,000 in annual savings for Nissan’s largest U.S. manufacturing facility — all while maintaining continuous vehicle production across their 4.7 million square foot plant.
$490,000
annual utility cost savings
8,500,000
kWh saved annually
location
Canton, MS
size
25,000 tons capacity
industry
Auto Manufacturing
the problem
Automotive Giant Seeks Energy Efficiency Solutions
Nissan’s Canton, Mississippi manufacturing facility, spanning 4.7 million square feet and home to the production of Altima, Titan, and Murano vehicles, faced significant energy efficiency challenges. The plant operated with a Primary/Secondary hydronic design that was inherently inefficient, and despite having a functional control system, it lacked optimization capabilities.
Plant controls were being managed manually, and corporate initiatives were pushing for reduced energy spending. The facility’s cooling system consisted of ten 2,500-ton chillers that weren’t operating at their optimal capacity.
the solution
Advanced Control Platform Transforms Manual Operations
tekWorx optimized the facility’s cooling operations through a comprehensive approach. At the heart of the transformation was the conversion to their innovative Integrated Primary-Secondary® (IPS) design, a patented hydronic architecture that eliminates inefficient bypass flow while maintaining critical redundancy and reliability. This architectural shift laid the groundwork for significant efficiency improvements through the implementation of Xpress® intelligent controls.
The team deployed the Xpress® optimization platform, specifically configured for Nissan’s existing PLC system, creating a seamless integration with their infrastructure. Xpress® continuously monitors system performance, environmental conditions, and load requirements to automatically adjust operational parameters in real-time, ensuring optimal efficiency regardless of changing demands or external factors.
The optimization project surpassed initial corporate energy goals, with a rapid 1.5 year payback, while maintaining zero production downtime throughout the facility-wide implementation.
the results
Strategic Investment Yields Multi-Million Dollar Impact
The facility achieved substantial cost reductions through energy efficiency improvements, resulting in $490,000 in annual savings and an impressive 1.5-year payback period. Most notably, the implementation reduced energy consumption by 8.5 million kWh annually, demonstrating the scale of efficiency gains possible through strategic optimization.
Beyond the financial metrics, the project delivered lasting operational benefits:
- Equipment lifecycle costs decreased significantly through reduced wear and tear on system components, extending asset longevity
- Operator efficiency improved as automated controls freed staff from manual system management for higher-value tasks
- System reliability increased through automated monitoring that enables proactive maintenance, reducing unexpected downtime
- Plant-wide efficiency improved through continuous real-time optimization of all cooling system components
The combination of immediate cost savings and long-term operational improvements created a sustainable solution that continues to generate value beyond the initial project goals.